Friction Stir Welding Market Size, Industry Trends, Revenue, Future Scope and Outlook 2030
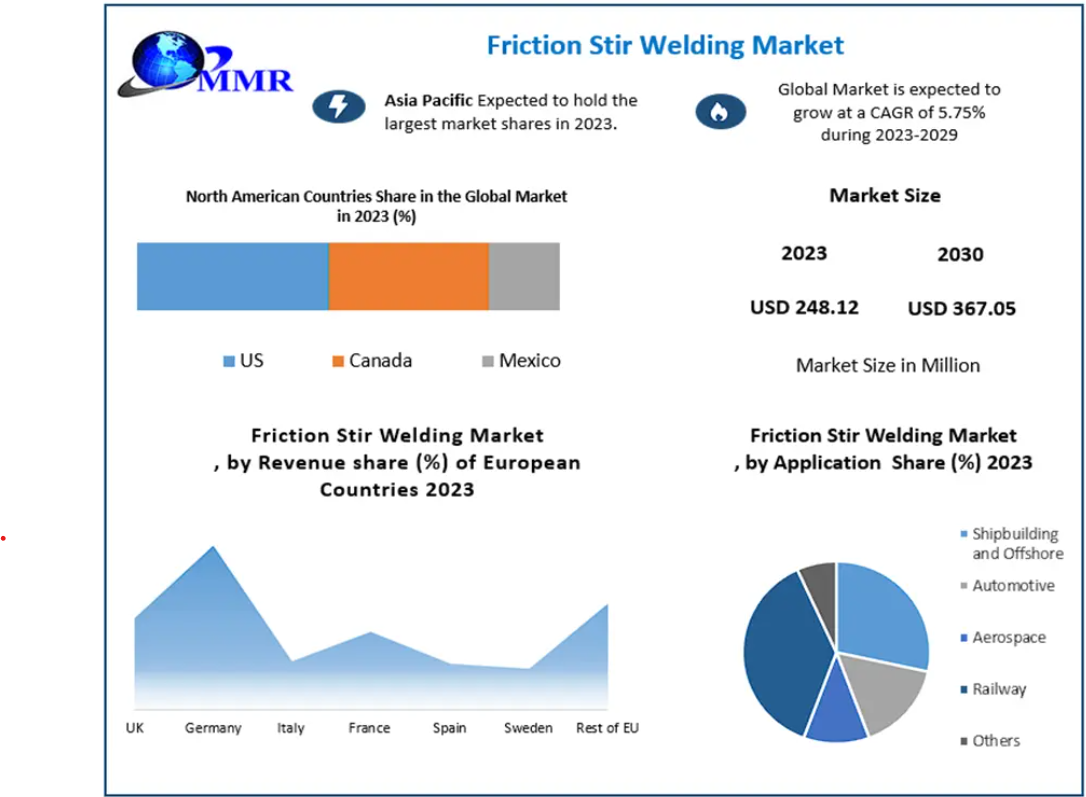
Global Friction Stir Welding Market Poised for Robust Growth, Projected to Reach USD 367 Million by 2030
The Global Friction Stir Welding Market is experiencing significant expansion, with projections indicating a rise from USD 248.12 million in 2023 to approximately USD 367.05 million by 2030, reflecting a compound annual growth rate (CAGR) of 5.75%. This growth is driven by advancements in welding technology, increasing demand for lightweight materials, and the expansion of applications across various industries.
Market Estimation & Definition
Friction stir welding is a solid-state joining process that utilizes a non-consumable tool to generate frictional heat, allowing materials to be joined without melting. This technique is particularly effective for welding aluminum and other lightweight materials, offering superior mechanical properties and reduced distortion compared to traditional welding methods.
In 2023, the global FSW market was valued at USD 248.12 million. With a projected CAGR of 5.75%, the market is expected to reach USD 367.05 million by 2030, underscoring the growing adoption of FSW technology across various sectors.
Ask for Sample to Know US Tariff Impacts on Friction Stir Welding Market @ Sample Link:https://www.maximizemarketresearch.com/request-sample/10856/
Market Growth Drivers & Opportunities
1. Demand for Lightweight Materials: The automotive and aerospace industries are increasingly utilizing lightweight materials like aluminum and magnesium to improve fuel efficiency and reduce emissions. FSW is ideal for joining these materials, driving its adoption in these sectors.
2. Enhanced Mechanical Properties: FSW produces joints with superior strength, fatigue resistance, and corrosion resistance, making it suitable for demanding applications in industries such as aerospace, automotive, and shipbuilding.
3. Environmental Benefits: FSW is an environmentally friendly welding technique as it does not require filler materials, reducing waste and energy consumption compared to traditional welding methods.
4. Technological Advancements: Continuous innovations in FSW technology, such as hybrid and laser-assisted FSW, are expanding its applicability and improving weld quality, further propelling market growth.
Segmentation Analysis
By Equipment Type:
- Fixed Friction Stir Welding: Dominating the market, fixed FSW machines offer stability and precision, making them suitable for high-volume production in industries like automotive and aerospace.
- Adjustable Friction Stir Welding: These machines provide flexibility, allowing adjustments to accommodate different material thicknesses and welding positions, catering to diverse manufacturing needs.
- Self-reacting Friction Stir Welding: Utilized for welding large, asymmetric components, these machines generate opposing forces to create a stable welding environment, essential for complex applications.
By Material:
- Aluminum Alloys: The most commonly welded materials using FSW, aluminum alloys are prevalent in automotive and aerospace applications due to their lightweight and strength properties.
- Magnesium: Used in applications requiring lightweight components, magnesium is increasingly being welded using FSW for its superior mechanical properties.
- Titanium: FSW is employed to join titanium in aerospace and medical applications, where strength and reliability are paramount.
- Copper: While challenging to weld, FSW enables the joining of copper for electrical and heat exchange applications.
- Steel Alloys: FSW is gaining traction in welding steel alloys, particularly in shipbuilding and structural applications, due to its ability to produce strong joints.
By Application:
- Automotive: FSW is extensively used in automotive manufacturing for joining lightweight materials, enhancing fuel efficiency and performance.
- Aerospace: The aerospace industry employs FSW for joining high-strength materials, ensuring the structural integrity of aircraft components.
- Shipbuilding: FSW is utilized in shipbuilding for welding large aluminum panels, offering improved strength and reduced weight.
- Railway: The railway sector adopts FSW for joining rail components, ensuring durability and resistance to fatigue.
- Others: FSW finds applications in various other sectors, including electronics, defense, and renewable energy, owing to its versatility and efficiency.
To know about the Research Methodology :-https://www.maximizemarketresearch.com/request-sample/10856/
Country-Level Analysis
United States:
The U.S. is a significant player in the global FSW market, driven by advancements in manufacturing technologies and the demand for lightweight materials in automotive and aerospace industries. The country's focus on innovation and infrastructure development further propels the adoption of FSW technology.
Germany:
Germany's FSW equipment market is experiencing steady growth, driven by the country's strong emphasis on precision engineering and technological advancements in manufacturing processes. Germany's automotive and aerospace industries are significant contributors to the demand for FSW, and the country's strategic investment in cutting-edge welding technologies is helping drive market growth.
Competitive Landscape
Key players in the FSW market are investing in research and development to enhance product offerings and expand their market presence. Notable developments include:
- Company A: Introduced a new generation of FSW machines tailored for automotive and aerospace industries, focusing on enhanced productivity and precision.
- Company B: Launched the Rebel™ FSW, a versatile welding device designed with adaptive control and automatic parameter optimization, catering to diverse material and thickness requirements.
These innovations underscore the commitment of industry leaders to advancing FSW technology and meeting the evolving demands of various sectors.
Conclusion
The global friction stir welding market is poised for substantial growth, driven by technological advancements, increasing demand for lightweight materials, and expanding applications across various industries. As sectors such as automotive, aerospace, and shipbuilding continue to prioritize efficiency and sustainability, FSW technology offers a viable solution for producing high-quality, durable joints. With ongoing innovations and strategic investments, the FSW market is set to play a pivotal role in shaping the future of manufacturing processes worldwide.